
Prototype CubeSat Structure
The CubeSat structure design is one of the fundamental considerations of our project. We decided to design and built the CubeSat structure in-house to help reduce costs and take advantage of the knowledgeable staff and equipment on campus. By designing and manufacturing our own structure, we can optimize its design to suit the user's specific needs. Follow our design process below!


Step 1:
The Initial Design
We first tried to answer what CubeSat users required through research and brainstorming. We then took what we learned and narrowed the list of features down to what is listed below.
-
The exterior dimensions must be 10 cm x 10 cm x 10 cm per NASA
-
Total mass must remain under 1.33 kg per NASA
-
The CubeSat structure must account for the following...
-
Stresses during launch such as shock and shear forces
-
Electromagnetic shielding
-
Provide protection for the internal components
-
Vibration
-
Temperature extremes
-
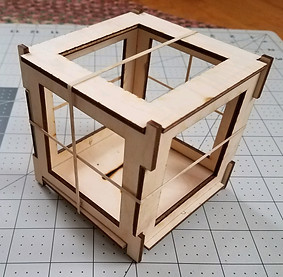
Step 2:
Manufacturing Prototypes
The main goal of this process was to produce a physical prototype structure. We used a CNC CO2 laser to precisely cut the CubeSat parts. The first prototype was cut from a luan sheet, which helped us gain a better understanding of the limitations of both our design and the laser cutter.
Learning about the different manufacturing methods and equipment was another very important aspect of this step. Being involved in and observing the production process helped us spot issues in the design that otherwise would have gone unnoticed.
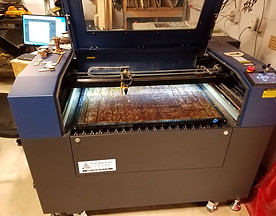
Step 3:
Evaluation and Redesign
During this step, we asked ourselves questions such as, "how can we make the structure design better suit the needs of the user?"
We also applied the lessons learned from the production process and asked ourselves, "how can we improve our design to simplify the production process?" It became evident that in order to produce an effective and quality minimum viable product, we needed to learn more about the manufacturing options available to us, such as machining.
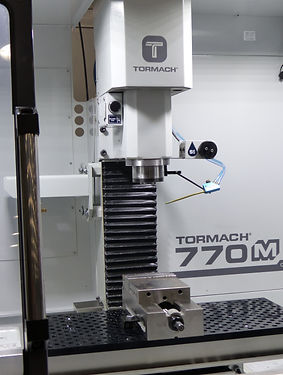